Solución a los problemas de medición de la deformación tras el tratamiento térmico
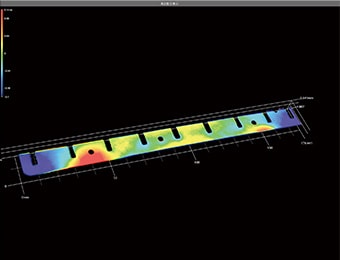
En términos generales, el tratamiento térmico es un proceso que aplica calor a materiales o productos. El tratamiento térmico incluye el procesado de materiales metálicos por calentamiento, así como la esterilización por calor de alimentos y otros productos. Esta sección examina la deformación del metal resultante del proceso de tratamiento térmico. Mientras que la deformación resultante del tratamiento térmico puede ser simple, como la compresión o la deformación en el caso de vigas y varillas cuadradas, la deformación tridimensional puede producirse en productos que tienen formas complejas. Esto requiere tecnologías avanzadas para medir estas formas.
En esta página se explican los conocimientos básicos sobre la deformación causada por los tratamientos térmicos que se utilizan con materiales de hierro o acero para controlar sus estructuras y mejorar sus propiedades. También aborda los problemas que plantea la medición de la deformación y algunas posibles soluciones.
- Tratamiento térmico de metales
- Ejemplos de deformación causada por el tratamiento térmico (cambio de volumen debido a la transformación de fase)
- Medidas para prevenir los problemas de deformación causados por el tratamiento térmico
- Problemas en la medición convencional de la deformación tras el tratamiento térmico
- Solución de problemas en la medición de la deformación tras el tratamiento térmico
- Resumen: mejoras espectaculares para medir la deformación tras el tratamiento térmico
Tratamiento térmico de metales
El tratamiento térmico de los metales es una técnica de transformación que calienta y enfría un metal para modificar sus propiedades sin cambiar su forma. Algunas de las propiedades que deben modificarse son la resistencia, la dureza, la tenacidad, la resistencia al impacto, la resistencia al desgaste, la resistencia a la corrosión, las propiedades de mecanizado y la trabajabilidad en frío.
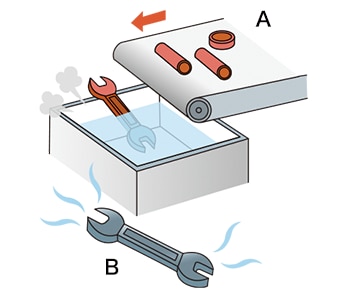
- A
- Calentamiento (hasta que el metal se vuelva rojo)
- B
- Enfriamiento (hasta que el metal calentado se vuelve negro)
Ejemplos de deformación causada por el tratamiento térmico (cambio de volumen debido a la transformación de fase)
Existen múltiples métodos de tratamiento térmico, como el temple, el revenido, el recocido y la normalización. Durante estos procesos, se produce un fenómeno conocido como transformación de fase.
La transformación de fase es un proceso que se produce durante el tratamiento térmico cuando un metal pasa de sólido a líquido y luego vuelve a pasar de líquido a sólido. Esto ocurre porque la forma actual (estructura) del metal cambia al modificarse su red cristalina como consecuencia de la temperatura. Cuando la estructura cambia durante la transformación de fase, el volumen también cambia, provocando la deformación.
Por ejemplo, cuando un acero eutectoide, que es un acero que contiene aproximadamente un 0.8% de carbono, se calienta desde la temperatura ambiente para crear una estructura de austenita y luego se enfría, se deforma debido al cambio de estructura. La estructura tras la transformación de fase varía en función del método de enfriamiento y, por lo tanto, el método de enfriamiento también afecta a la cantidad de deformación.
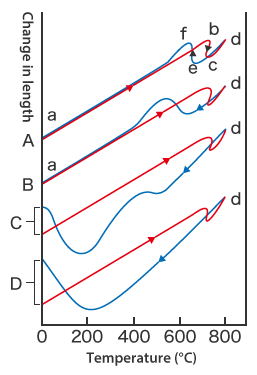
Este gráfico muestra las diferencias de deformación resultantes de los distintos métodos de enfriamiento.
En el caso de A, el metal se expande como resultado del calentamiento (a → b), y pueden observarse cambios en sus dimensiones debidos a la transformación de fase a aproximadamente 750°C (1382℉) durante el calentamiento (b → c) y a aproximadamente 730°C (1346℉) durante el enfriamiento (e → f).
En C (enfriamiento por aceite) y D (enfriamiento por agua), hay un claro cambio de longitud tras la refrigeración.
- A: Enfriamiento del horno (enfriamiento lento)
- El metal se mantiene en el horno después del calentamiento y se enfría mientras está dentro del horno. Este método enfría el metal a una velocidad aproximada de 30°C (54℉) por hora. La estructura tras la transformación de fase es perlita.
- B: Enfriamiento por aire
- El metal se retira del horno tras el calentamiento y se enfría a temperatura ambiente. La estructura tras la transformación de fase es sorbita.
- C: Enfriamiento por aceite
- El metal calentado se enfría en aceite. Normalmente, el metal se enfría en aceite a aproximadamente 60 a 80°C (140 a 176℉). En la estructura después de la transformación de fase, parte de la estructura de austenita se transforma en troostita.
- D: Enfriamiento por agua
- El metal se enfría en agua a unos 40°C (104℉). La estructura tras la transformación de fase es martensita.
Medidas para prevenir los problemas de deformación causados por el tratamiento térmico
Además de la transformación de fase descrita en la sección anterior, otras razones de los problemas de deformación causados por el tratamiento térmico son la forma incorrecta o desigual de la superficie o el calentamiento/enfriamiento. En esta sección se explican estos problemas de deformación, sus causas y las medidas para evitarlos.
Grietas de enfriamiento
Se trata de un problema en el que se produce el agrietamiento del material. Puede producirse al día siguiente del enfriamiento rápido o más tarde, después de que el material se haya enfriado a aproximadamente 200°C (392℉) o menos.
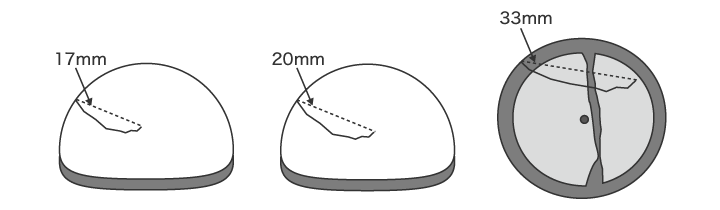
- Causas:
- Entre las posibles causas se encuentran los defectos de forma causados por la expansión de volumen debida a un calentamiento o enfriamiento desigual, un revenido inadecuado inmediatamente después del temple y una temperatura de temple excesivamente alta.
- Contramedidas:
-
- Revise la forma del producto y las condiciones de la superficie.
- No enfríe los materiales templados a aproximadamente 200°C (392℉) o menos.
- Realizar el templado de los materiales inmediatamente después del enfriamiento rápido.
- Bajar la temperatura de enfriamiento.
Grietas por rectificado
Se trata de un problema en el que se produce el agrietamiento del material de acero cuando se rectifica después del tratamiento térmico. Existen dos tipos de grietas de esmerilado: Grietas de esmerilado de tipo 1, que se producen cuando una superficie mecanizada por corte, pulido u otro método alcanza aproximadamente 100°C (212℉), y grietas de esmerilado de tipo 2, que se producen cuando una superficie mecanizada por corte, pulido u otro método alcanza aproximadamente 300°C (572℉).
-
Grieta de esmerilado de tipo 1
-
Grieta de esmerilado de tipo 2
- Causas:
- La austenita residual se expande cuando se transforma en martensita. La tensión causada por esta expansión provoca la fisuración del material. Esta deformación también puede producirse cuando una superficie mecanizada por corte, pulido u otro método alcanza aproximadamente de 650 a 850°C (1202 a 1562℉).
- Contramedidas:
-
- Realizar el templado adecuado.
- Reducir el calor generado por la fricción del rectificado.
Deformación por enfriamiento
Existen dos tipos de deformación del acero provocada por el tratamiento térmico: la deformación térmica causada por la expansión o contracción térmica durante el temple o revenido, y el cambio de volumen provocado por la transformación de fase.
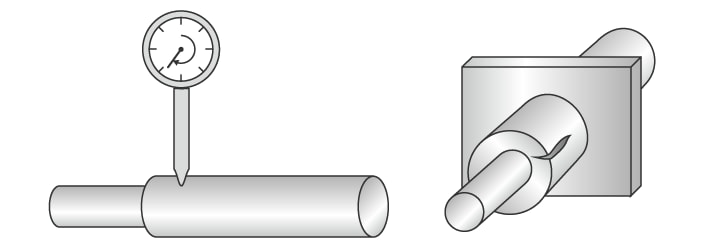
- Causas:
- Esta deformación se produce como resultado de un calentamiento o enfriamiento desigual, un calentamiento o enfriamiento rápido o piezas de espesor desigual. Cuando un material tiene una forma compleja, una distribución desigual de la temperatura en el material también puede provocar esta deformación.
- Contramedidas:
-
- Revise la forma para que el producto pueda calentarse y enfriarse uniformemente.
- Reduzca las velocidades de calefacción y refrigeración.
Problemas en la medición convencional de la deformación tras el tratamiento térmico
Es sumamente importante comprobar que las dimensiones y formas tras el tratamiento térmico se ajustan a las tolerancias. En particular, los productos con formas complejas requieren una medición cuantitativa de formas 3D de alta precisión.
La medición convencional de la deformación tras el tratamiento térmico utiliza sistemas de medición de perfiles o máquinas de medición de coordenadas. Sin embargo, la medición con una máquina de medición de coordenadas convencional o un sistema de medición de perfiles plantea diversos problemas. Entre ellas se incluyen el alto nivel de dificultad necesario para obtener mediciones precisas y la variación de los valores medidos.
Problemas en la medición de deformaciones mediante un sistema de medición de perfiles
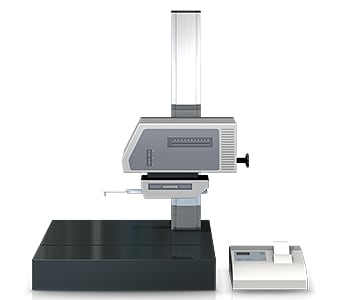
Un sistema de medición de perfiles mide y registra el perfil de un objetivo trazando su superficie con un lápiz óptico. En los últimos años, se han desarrollado sistemas de medición de perfiles que utilizan un láser en lugar de un lápiz óptico para medir formas complejas trazando el perfil sin contacto. Algunos modelos son incluso capaces de realizar mediciones tanto de la superficie superior como de la inferior.
Sin embargo, con un sistema de medición de perfiles, es necesario adquirir líneas de medición precisas para los puntos de medición.
Esto plantea los siguientes problemas.
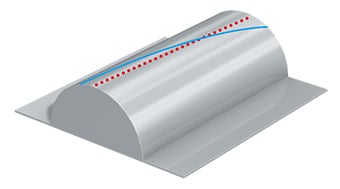
- El trabajo de medición requiere mucho tiempo, incluido el tiempo necesario para fijar la muestra a la plantilla y nivelarla. También se requieren conocimientos y habilidades relacionados con el uso de sistemas de medición de perfiles para nivelar un objetivo con precisión.
- El lápiz óptico de un sistema de medición de perfiles se mueve hacia arriba y hacia abajo en un arco centrado en el fulcro del brazo del lápiz óptico, y la punta del lápiz óptico también se mueve en la dirección del eje X. Esto produce error en los datos del eje X.
- Trazar la línea deseada con el lápiz óptico es un trabajo extremadamente difícil, e incluso un ligero desplazamiento del lápiz óptico produce errores en los valores medidos.
- También es difícil aumentar el número de objetivos debido a la necesidad de señalar lugares específicos para la medición.
- Solo se puede medir una parte del objetivo, y no es posible evaluar toda la superficie.
Problemas en la medición de deformaciones con una máquina de medición de coordenadas
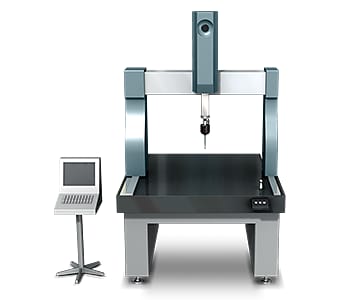
Las típicas máquinas de medición de coordenadas utilizan una sonda para escanear o trazar una superficie y recopilar varios puntos de datos en un paso especificado.
Este método de medición plantea los siguientes problemas.
- Garantizar que la sonda se desplaza según lo previsto es una tarea extremadamente difícil, sobre todo en el caso de líneas rectas a lo largo del centro de un cilindro o de una superficie curva, o de líneas que pasan por el centro de un círculo. Si un filete o redondeo tiene un ángulo central amplio, como todo el círculo se calcula a partir de un arco corto, incluso un pequeño error de medición se magnificará en gran medida. Estas desviaciones en los puntos de medición pueden provocar ligeras variaciones en los valores medidos.
- Al medir una forma 3D pequeña, es posible que la sonda no pueda entrar en contacto con las posiciones de medición. Dado que la precisión de la medición es proporcional al número de puntos o líneas que se miden, es necesario medir un gran número de puntos o líneas.
De este modo, la medición mediante una máquina de medición de coordenadas conlleva importantes problemas, como el hecho de que no todos los operadores del lugar de trabajo pueden medir con precisión las formas, la existencia de piezas que no pueden medirse en absoluto y la limitación de los lugares en los que puede instalarse la máquina.
Solución de problemas en la medición de la deformación tras el tratamiento térmico
Estos instrumentos de medición pueden tener problemas con el posicionamiento de un objeto o de la punta de la sonda, y pueden tener dificultades para proporcionar datos de medición globales de una superficie tridimensional, ya que se limitan a medir por puntos o líneas. Para resolver estos problemas, KEYENCE ha desarrollado el perfilómetro óptico 3D de la Serie VR.
La Serie VR captura con precisión la forma 3D de toda la superficie del objetivo en tan solo un segundo y sin entrar en contacto con el objetivo. Es capaz de cuantificar de forma instantánea y precisa toda una superficie 3D sin errores de medición. Esta sección presenta algunas ventajas específicas de la Serie VR.
Ventaja 1: medir un gran número de puntos en tan solo un segundo
La Serie VR adquiere datos de superficie (800,000 puntos) de la forma del objetivo 3D en tan solo un segundo, lo que reduce drásticamente el tiempo necesario para medir un gran número de puntos. Mide de forma precisa e instantánea las irregularidades máximas y mínimas de toda la superficie del objetivo, lo que permite una evaluación rápida de todos los puntos del objetivo en función de las tolerancias preestablecidas.
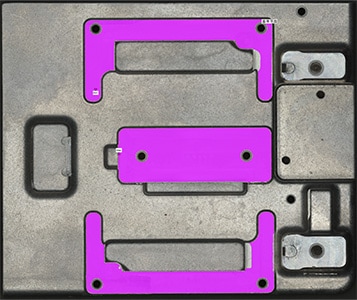
Una vez escaneada una pieza, su perfil (sección transversal) también puede medirse en ubicaciones distintas de las utilizadas en la medición anterior. Esto elimina la necesidad de fijar y medir de nuevo el mismo objetivo.
Ventaja 2: los datos medidos pueden compararse con datos de referencia
La Serie VR es capaz de mucho más que recopilar datos de forma eficiente. Los datos de medición pueden visualizarse en una lista y puede aplicarse el mismo contenido de análisis a todos los datos al mismo tiempo.
Es posible comprobar rápidamente las diferencias en los datos obtenidos midiendo múltiples formas objetivo antes y después del tratamiento térmico, y la cantidad de diferencia en los productos malos cuando se comparan con el producto de referencia. Esto permite un fácil análisis cuantitativo y la evaluación de la deformación causada por el tratamiento térmico.
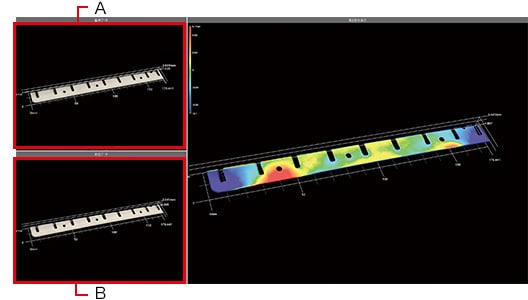
- A
- Datos de referencia
- B
- Datos de medición
La Serie VR puede medir rápidamente objetivos que tienen formas complejas, algo que antes habría requerido mucho tiempo y trabajo. No solo se capturan rápidamente los datos, sino que todos los resultados de las mediciones se digitalizan, lo que reduce considerablemente el trabajo necesario para comparar y analizar los datos.
Resumen: mejoras espectaculares para medir la deformación tras el tratamiento térmico
Antes, medir la deformación causada por el tratamiento térmico llevaba mucho tiempo, lo que limitaba el número de muestras que podían medirse. En algunos casos, la medición no fue posible en absoluto debido a la compleja forma de la pieza. Sin embargo, la Serie VR es capaz de medir y cuantificar rápidamente la deformación de estas formas. Como resultado, la Serie VR puede evaluar la calidad del producto con un mayor nivel de precisión y eficacia.
- Reduzca considerablemente el tiempo dedicado a la medición de formas complejas capturando simultáneamente los datos de toda la superficie.
- Las distintas diferencias de deformación pueden identificarse y analizarse fácilmente capturando y comparando varios conjuntos de datos de medición.
- Es posible realizar una verdadera medición cuantitativa, eliminando la variación de los resultados debida a errores humanos.
- Basta con colocar el objetivo en la plataforma y presionando un botón para capturar datos precisos, eliminando la necesidad de operadores especializados, ya que no es necesario posicionarlo ni realizar ningún otro tipo de preparación.
- Mida con precisión muchos objetivos en poco tiempo con el escaneado de alta velocidad.
La Serie VR también es capaz de comparar datos con escaneados anteriores y modelos CAD, así como de analizar la rugosidad.