Medición sencilla y precisa de componentes de chips
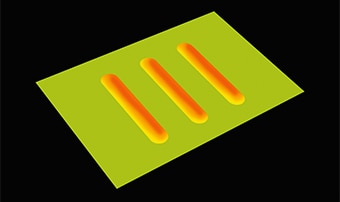
Las recientes tecnologías de montaje de placas de circuito impreso (PCB) son cada vez más densas y complejas en respuesta a la necesidad de terminales de información más pequeños, ligeros y finos, como los teléfonos inteligentes y la electrónica doméstica, y también de componentes electrónicos más pequeños, como resistencias de chip y condensadores cerámicos. Esta sección presenta los problemas que pueden surgir con los componentes montados, así como el modo en que los sistemas de medición 3D pueden utilizarse para evaluar, analizar y prevenir estos problemas.
- Método de montaje de componentes de chip
- ¿Qué es la soldadura por refusión?
- Control de temperatura del horno de refusión
- Problemas en el montaje superficial
- Ejemplo de medición de deformación de la placa del circuito
- Ejemplo de medición de la coplanaridad de las terminales de un condensador electrolítico de aluminio
- Ejemplo de medición del espesor de la pasta de soldadura
- Ejemplos de medición del espesor de película resistiva
- Ejemplo de medición en profundidad de grietas en láminas
- Medición de anchura dieléctrica
Método de montaje de componentes de chip
Junto con la miniaturización de los componentes electrónicos y la mayor densidad de montaje en las PCB, la soldadura por refusión se ha convertido en la más predominante.
Método de soldadura | Características | |
---|---|---|
Ventajas | Desventajas | |
Soldador |
Baja tensión térmica |
Gran fluctuación de la temperatura |
Aire caliente |
Baja tensión térmica |
Gran fluctuación de la temperatura |
Láser |
|
No es adecuado para la producción en masa (largo tiempo de procesamiento) |
Pulso de calor |
|
No es adecuado para la producción en masa (largo tiempo de procesamiento) |
Refusión (tipo infrarrojo) |
|
|
Refusión (tipo de aire caliente) |
|
|
Soldadura por ola |
|
|
¿Qué es la soldadura por refusión?
La pasta de soldadura, que es una mezcla uniforme de soldadura en polvo y fundente, se aplica sobre una placa metálica con agujeros perforados y se extiende en una capa fina con una espátula para hacer una impresión. Los componentes se montan después en la placa de circuito, se calientan y se sueldan.
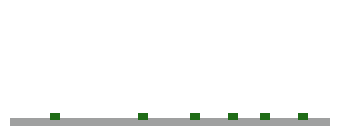
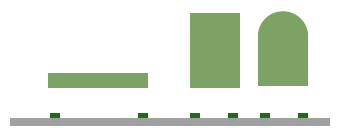
Si el número de componentes es pequeño, también es posible realizar el montaje de componentes a mano.
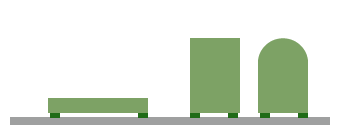
La temperatura se controla en cinco etapas (consulte la sección a continuación).
Control de temperatura del horno de refusión
El calor se aplica normalmente en dos etapas. En la primera etapa de calentamiento, la placa de circuito se lleva y mantiene a una temperatura uniforme. En la segunda etapa de calentamiento, la pasta de soldadura se funde. La temperatura y el tiempo de calentamiento varían dependiendo del tipo de horno de reflujo y los componentes utilizados.
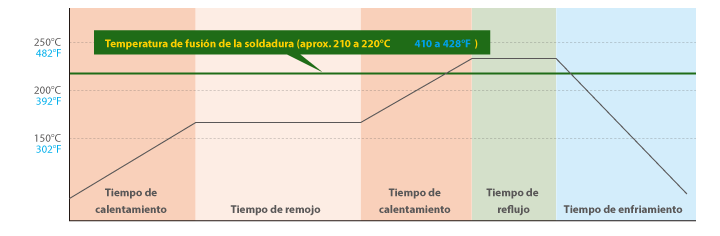
Problemas en el montaje superficial
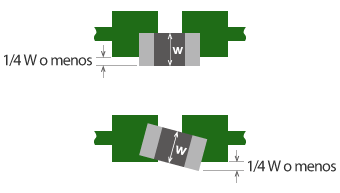
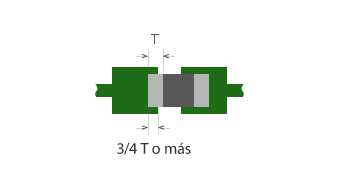
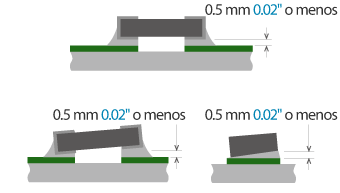
Ejemplo de medición de deformación de la placa del circuito
La deformación de la PCB es causada por cambios de temperatura que ocurren cuando se suministra energía o por cambios ambientales. Se realiza un análisis para determinar si se han producido defectos debido a estos cambios de temperatura. La deformación causada por las fluctuaciones de temperatura se puede medir desde la temperatura ambiente hasta 260°C a 500°F.
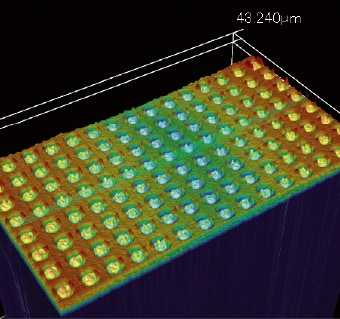
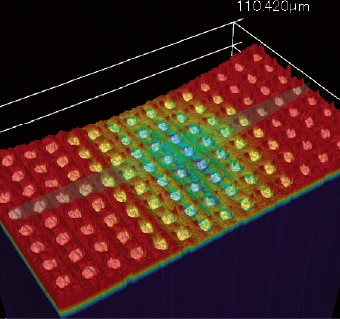
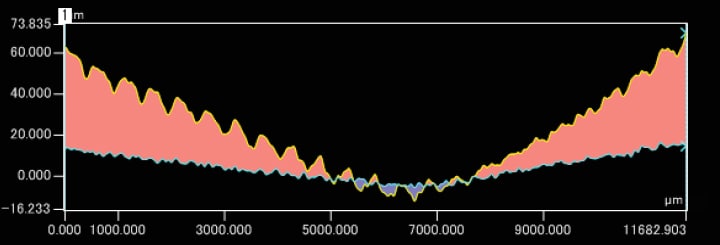
Ejemplo de medición de la coplanaridad de las terminales de un condensador electrolítico de aluminio
Se puede medir la planicidad de los terminales de condensadores, que pueden provocar defectos de montaje en la PCB e influir en la resistencia de montaje de las PCB.
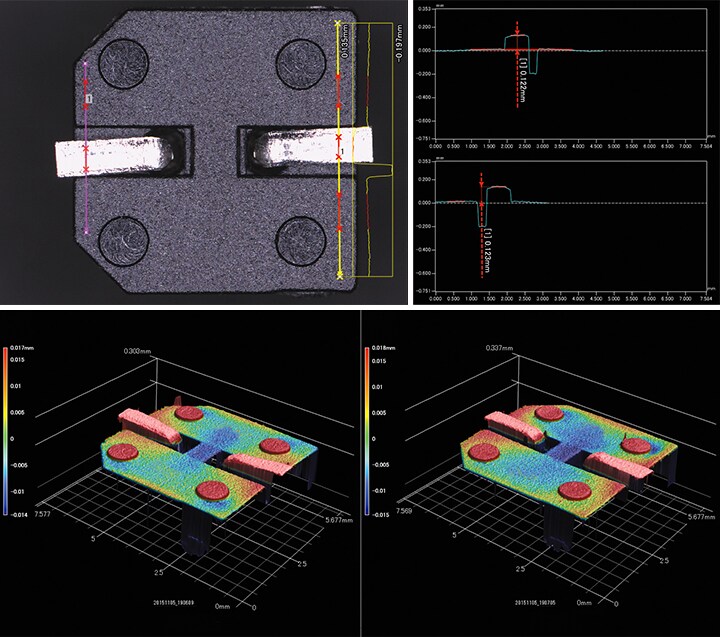
Ejemplo de medición del espesor de la pasta de soldadura
Se puede medir el espesor de la capa de soldadura aplicada a una PCB.
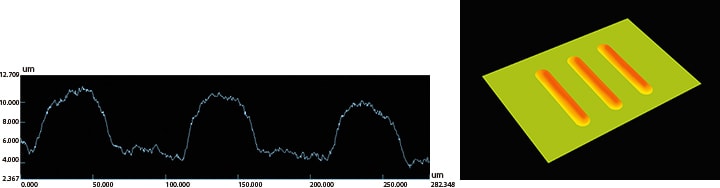
Ejemplos de medición del espesor de película resistiva
El espesor y el volumen de una película resistiva en estado húmedo pueden medirse antes de la sinterización, una vez impresa la película.
El espesor de la película puede medirse mientras está húmeda, por lo que las condiciones para el proceso de sinterización pueden establecerse eficazmente.
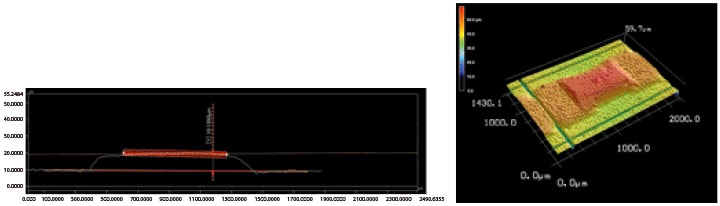
Estructura de resistencia de chip
Las resistencias chip son pequeñas resistencias fijas cuadradas que constan de un elemento resistivo formado en la superficie de una base aislante, como la cerámica, con electrodos en ambos extremos. Son adecuados principalmente para el montaje en superficie.
Estructura típica de una resistencia de chip cuadrada
- (1) No hay cable conductor en los electrodos terminales
- (2) Es posible soldar o pegar
* También existen resistencias de tipo MELF con forma cilíndrica, pero no se suelen utilizar.
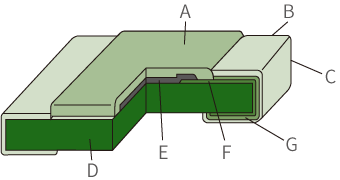
- A
- Película protectora
- B
- Revestimiento exterior
- C
- Electrodo terminal
- D
- Cerámica
- E
- Película resistiva
- F
- Electrodo interno
- G
- Niquelado
- Cerámica (base)
- La base está hecha de una placa de cerámica para soportar la sinterización o el recorte del elemento resistivo.
- Elemento resistivo
- Los hay de película gruesa y de película fina.
- Electrodo
- El elemento resistivo está conectado a los electrodos terminales a través de electrodos internos. Tiene una estructura de al menos tres capas.
- Película protectora
- La superficie del elemento resistivo está recubierta con resina o vidrio, para evitar la adhesión directa de humedad o polvo.
Ejemplo de medición en profundidad de grietas en láminas
La longitud y la profundidad de las películas pueden medirse para garantizar que las resistencias de chip se mantienen dentro de las especificaciones.
También pueden medirse la anchura y la profundidad de las grietas que se producen en las zonas recortadas.
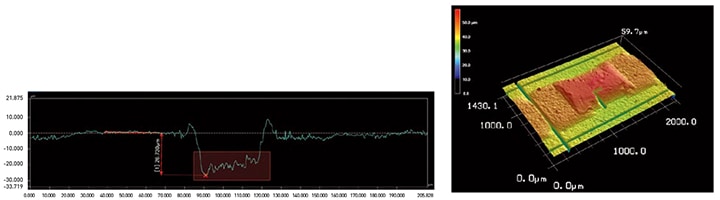
Corte láser
Las capas de una resistencia de chip se forman mediante serigrafía. Dado que varios cientos de elementos resistivos se forman sobre una base cerámica, incluso variaciones mínimas en las condiciones de impresión provocan directamente variaciones en la resistencia.
Si la resistencia varía entre resistencias de chip, sus características eléctricas no satisfarán su clasificación. Esto lleva a la necesidad de realizar un corte láser para ajustar la resistencia. El corte por láser consiste en medir uno a uno los elementos resistivos y recortarlos para garantizar la resistencia especificada y minimizar las variaciones.
- (1) Los elementos resistivos se imprimen buscando una resistencia ligeramente inferior a la resistencia objetivo.
- (2) Recortar un elemento resistivo hace que su paso de corriente sea más estrecho, lo que aumenta la resistencia.
- (3) El corte se detiene cuando se alcanza la resistencia objetivo para minimizar la fluctuación entre las virutas.
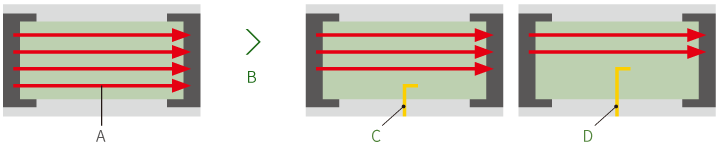
- A
- Flujo de corriente eléctrica
- B
- Recorte láser
- C
- Una longitud corta del recorte provoca un pequeño cambio en la resistencia.
- D
- Una longitud larga del recorte provoca un gran cambio en la resistencia.
* A medida que se recorta más el elemento, el recorrido de la corriente en el elemento resistivo se hace más estrecho, lo que aumenta la resistencia.
La longitud y la forma finales del corte se determinan en función de la variación de la resistencia durante el recorte.
Cuando se comparan los cambios de la resistencia basados en la longitud de corte, entre corte recto y corte en forma de L, resulta que el corte en forma de L puede proporcionar una mayor precisión en el corte final, y reducir la influencia de las microfisuras en el extremo.
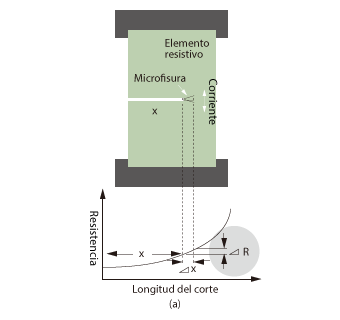
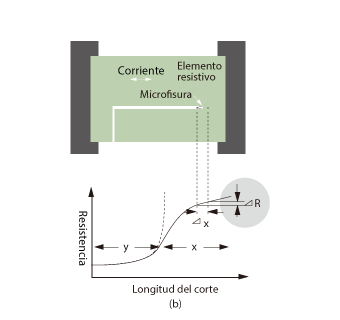
Medición de anchura dieléctrica
Se puede medir la anchura y espesor de un dieléctrico en estado húmedo.
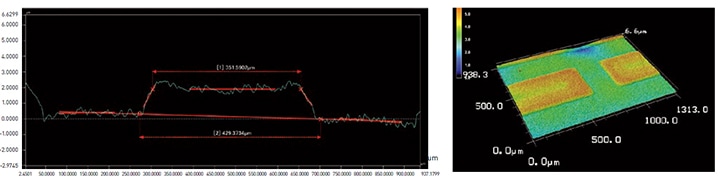
Estructura de un condensador de chip cerámico multicapa
La estructura básica de un condensador consiste en un dieléctrico entre dos placas de electrodos.
- (1) El material dieléctrico, como el titanato de bario (BaTiO3), un dieléctrico cerámico, se aplica a una película portadora.
- (2) El material se seca para crear una lámina fina.
- (3) Se imprime en la lámina una pasta de material de electrodo que contiene metales como paladio, plata o níquel.
- (4) Las láminas se apilan en 10 a 1000 capas, se prensan y se cortan en virutas.
- (5) Los últimos pasos en la creación de condensadores de chip cerámicos multicapa son la sinterización y el chapado en plata de las terminales externas.
Las virutas se encogen alrededor de un 10 % durante la sinterización de la cerámica, lo que es importante tener en cuenta a la hora de determinar sus dimensiones.
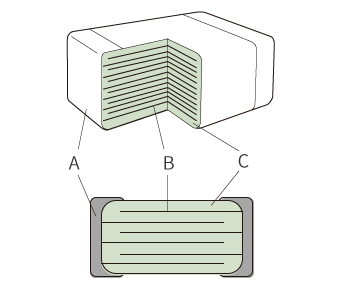
- A
- Electrodo externo
- B
- Electrodo interno
- C
- Dieléctrico de cerámica
Relación proporcional entre la capacitancia electrostática y el área de la placa del electrodo
Conectar varios condensadores en paralelo equivale a aumentar el área del electrodo, por lo que puedes aumentar la capacitancia electrostática aumentando el número de condensadores.
El uso de varios condensadores ocupará un gran volumen en la placa de circuito, por lo que este método no es apropiado cuando se necesita ahorrar espacio.
Para evitarlo, los condensadores de chip cerámicos multicapa logran tanto la miniaturización como una gran capacidad al tener estructuras multicapa de dieléctricos cerámicos y electrodos internos apilados alternativamente.