Medición del paralelismo de productos conformados a presión
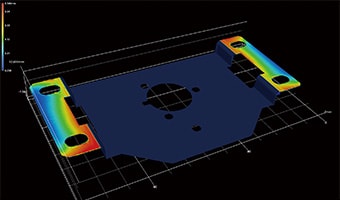
El prensado es un tipo de trabajo del plástico; en algunos casos de prensado del plástico puede que la forma no sea la diseñada. Suele producirse cuando la tensión permanece en el interior del material después del prensado debido a factores como el rebote. Es necesario tener precaución al conformar la lámina en forma de manivela o en forma de U mediante plegado, ya que las esquinas pueden no formar los ángulos prescritos y el paralelismo puede desviarse de las tolerancias designadas. En la fabricación de bastidores de automóviles, la norma de resistencia a la tracción de la lámina de acero se ha elevado en los últimos años, lo que dificulta el prensado de alta precisión.
Esta sección explica los problemas con el paralelismo en el prensado explicando los conocimientos sobre la medición del paralelismo, los problemas en la medición del paralelismo y una solución a estos problemas.
- Causa del error de paralelismo: rebote
- Problemas en la medición convencional del paralelismo
- Solución de problemas en la medición del paralelismo
- Resumen: mejora integral y mayor eficacia para problemas en la medición del paralelismo de productos conformados en prensa
Causa del error de paralelismo: rebote
El paralelismo de la superficie de apoyo y de deslizamiento de la máquina de prensado, así como el paralelismo del producto conformado, son extremadamente importantes en el prensado. Cuando el paralelismo de la superficie del cabezal y de la corredera no es correcto, el ángulo de plegado y el soporte de la pieza bruta de dibujo se verán afectados incluso cuando la corredera se mueva verticalmente. Esto reduce la vida útil del troquel. Los fallos de paralelismo de los productos conformados tras el prensado se producen principalmente como resultado de la tensión residual (tensión interna) que existe en el interior del producto conformado. Esta deformación se denomina rebote, y es una de las razones por las que resulta difícil mantener la precisión dimensional requerida durante el prensado.
Tipos de rebote
Las causas del rebote pueden identificarse investigando las condiciones de tensión interna dentro del producto formado en la posición de punto muerto inferior de la prensa. En el punto muerto inferior durante la flexión, la tensión de tracción se produce en el exterior de la curva y la tensión de compresión se produce en el interior de la curva. La separación del troquel se produce cuando hay diferencias de tensión en la dirección del espesor de la lámina, lo que en última instancia modifica el ángulo. Los tipos típicos de rebote incluyen el cambio de ángulo o la deformación de la pared vertical en la parte redondeada del hombro del troquel, la torsión y la deformación de la línea de cresta. A continuación se explican las tensiones que provocan el rebote y ejemplos de defectos de rebote.
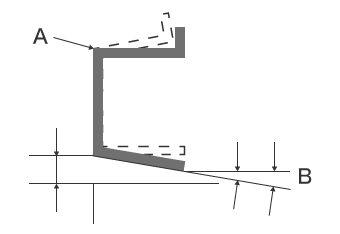
- A
- Línea de cresta curvada
- B
- Cambio de ángulo
- Cambio de ángulo:
- Se trata de un defecto en el que el ángulo de curvatura cambia debido a diferencias de tensión en la dirección del espesor de la lámina.
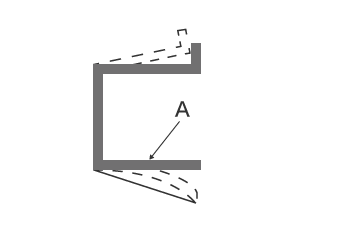
- A
- Deformación de la pared
- Deformación de la pared:
- Se trata de un defecto en el que la pared se deforma debido a diferencias de tensión en la dirección longitudinal.
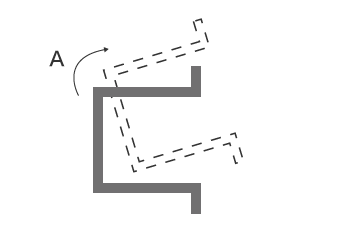
- A
- Torsión
- Torsión:
- Se trata de un defecto en el que toda la pieza se tuerce debido a las diferencias de tensión en la dirección del espesor de la lámina y a la tensión que actúa hacia el interior de la superficie.
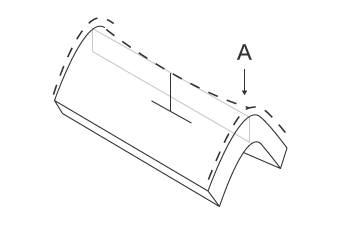
- A
- Deformación de la línea de cresta
- Deformación de la línea de cresta:
- Se trata de un defecto en el que la línea de cresta de flexión se deforma debido a las diferencias de tensión en la dirección del espesor de la lámina.
Contramedidas contra el rebote del paralelismo
Las medidas para contrarrestar el rebote suelen consistir en cambiar el diseño o la forma del troquel en la dirección opuesta a la dirección en la que se produce el rebote. Ajustando la cantidad de retroceso por muelle y la dirección del rebote en el troquel de prensado, es posible conseguir las tolerancias dimensionales.
Antes, las contramedidas contra el rebote dependían en gran medida de la intuición y la experiencia del diseñador, y la modificación del troquel se realizaba después de las pruebas. Sin embargo, dado que el retroceso elástico tiende a aumentar en proporción a la resistencia a la tracción de la lámina de acero, puede ser necesario realizar un gran número de modificaciones en el troquel en los casos en los que exista un gran rebote. Para resolver este problema, en el diseño de matrices se utilizan recientemente simulaciones mediante el método de los elementos finitos (MEF).
También existen otras contramedidas, como el "curvado en dos pasos", que realiza el curvado dos veces con una sola pasada de la máquina. Además, el "golpeado" añade salientes en ambas esquinas del filo de corte del punzón y el "mecanizado de ranuras" crea una hendidura en forma de V (muesca en V) por adelantado en la parte del material mecanizado que se curva.
Estas contramedidas pueden emplearse cuando se conoce la causa del rebote. Dado que las formas de los productos conformados a presión reales son complicadas, puede resultar muy difícil identificar la causa del rebote. Por este motivo, se necesita un método más eficaz para calcular el rebote.
Cálculo del rebote
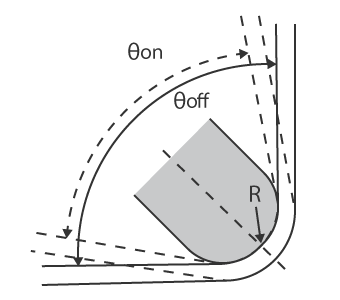
Si se puede hacer un cálculo, aunque sea aproximado, de la cantidad de rebote, entonces será posible adoptar contramedidas antes del mecanizado. Sin embargo, la fórmula de cálculo para predecir la cantidad de rebote es complicada y, en general, se utiliza en el momento del diseño del troquel. Como referencia, la fórmula se muestra a continuación.

- Δθ
- Cambio de ángulo resultante del rebote
- θon
- Ángulo de flexión (°) al aplicar presión
- θoff
- Ángulo de flexión (°) después del rebote
- σB
- Resistencia de la lámina de acero (N/mm2)
- R
- Radio de curvatura del punzón (mm)
- E
- Módulo de Young de la lámina de acero (= 206,000 N/mm2)
- t
- Espesor de la lámina de acero (mm)
* σB (resistencia de la lámina de acero) y E (módulo de Young de la lámina de acero) son valores inherentes al material.
El filo de corte para el plegado se crea en función de la cantidad estimada de rebote. Es difícil seguir calculando el error resultante del rebote. En otras palabras, es más fácil ajustar el radio interior que calcular la cantidad de rebote. Además, existe un gran error entre el valor calculado y el valor real debido a los efectos de factores como la variación del espesor de la lámina y las diferencias en las especificaciones de la máquina. Por eso es necesario confirmar la tolerancia dimensional midiendo después del conformado.
Problemas en la medición convencional del paralelismo
El paralelismo es un valor que indica el grado de paralelismo de cada plano o línea de un producto formado con respecto al plano o línea virtual perfecta de referencia. Se mide fijando un plano o una línea virtual, y no puede medirse con una herramienta manual como un calibrador o un micrómetro. Por este motivo, el paralelismo de un producto prensado se mide con una máquina de medición de coordenadas o un instrumento de medición de imágenes CNC. Sin embargo, la medición del paralelismo con estos instrumentos requiere conocimientos técnicos precisos y avanzados, así como experiencia, e implica los siguientes problemas de medición.
Problemas en la medición del paralelismo con una máquina de medición de coordenadas
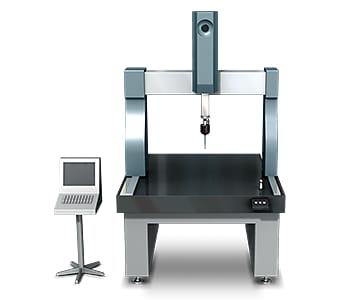
En general, para medir deformaciones con una máquina de medición de coordenadas, es necesario que el lápiz óptico entre en contacto con cuatro o más esquinas de la superficie medida del objetivo.
Por ejemplo, cuando se mide un plato, generalmente se miden entre seis y ocho puntos. Cuando el área de medición es grande, la precisión de la medición puede mejorarse aumentando el número de puntos medidos para recopilar más datos de medición.
Sin embargo, cuando se utiliza una máquina de medición de coordenadas para la medición del paralelismo surgen los siguientes problemas.
- Dado que es necesario medir por contacto puntos individuales, resulta fundamentalmente difícil identificar la forma completa.
- Dado que medir más puntos para adquirir más datos de medición requiere mucho tiempo, no es posible identificar la forma detallada de todo el objetivo.
Problemas en la medición del paralelismo con un instrumento de medición de imágenes CNC
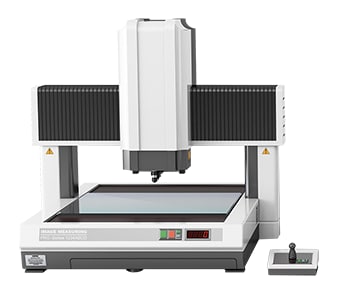
En general, un instrumento de medición de imágenes capta el objetivo en el escenario mediante una cámara CCD y realiza la medición en 3D. La observación mediante imágenes en color es posible, pero existen los siguientes problemas cuando se utilizan para medir el paralelismo.
- La detección falsa puede producirse cuando hay protuberancias en el objetivo. Además, cuando los puntos de medición u otros ajustes son diferentes, se producen variaciones en la precisión de la medición.
- Cuando aumenta el número de elementos de medición X, Y, Z o de otro tipo, el programa se vuelve complejo y requiere tanto conocimientos avanzados de expertos como horas de trabajo para su configuración. Las horas-hombre de medición necesarias aumentan en proporción al número de objetivos de medición. Existen problemas importantes, como la necesidad de una cámara de medición, la necesidad de mantener la cámara de medición a la temperatura de referencia y el hecho de que no todos los operadores del lugar de trabajo pueden realizar mediciones precisas.
Solución de problemas en la medición del paralelismo
Las máquinas de medición de coordenadas que se utilizan habitualmente requieren mucho tiempo para realizar la medición porque miden objetivos tridimensionales y ubicaciones de medición realizando mediciones por contacto de múltiples puntos. Además, con este tipo de herramientas se observan problemas como la escasa fiabilidad de los valores medidos debido a las variaciones causadas por factores humanos y la dificultad para crear datos utilizables a partir de los números, las funciones de análisis y otras técnicas de postprocesamiento.
Para resolver estos problemas de medición, KEYENCE ha desarrollado el perfilómetro óptico 3D de la Serie VR y la CMM con escáner 3D de la Serie VL.
Estos productos capturan con precisión la forma tridimensional de toda la superficie del objetivo sin entrar en contacto con él. También miden la forma tridimensional escaneando el objetivo en el escenario en tan solo un segundo con gran precisión. Esta sección presenta algunas ventajas específicas de estos sistemas.
Ventaja 1 de la Serie VR: se pueden medir hasta 800,000 puntos en una sola exploración, lo que elimina la necesidad de repetir la medición.
La VR-6000 puede capturar hasta 8000 000 puntos de datos en toda una superficie (área de 12" × 6") en tan solo un segundo. Dado que la medición no se realiza mediante líneas o puntos, no es necesario repetir la medición, lo que reduce el tiempo total dedicado a realizar mediciones. La medición que requiere datos como el paralelismo o la perpendicularidad también es fácil. Los datos medidos se almacenan automáticamente, y los datos almacenados pueden compararse con otros datos o con datos de diseño en 3D.
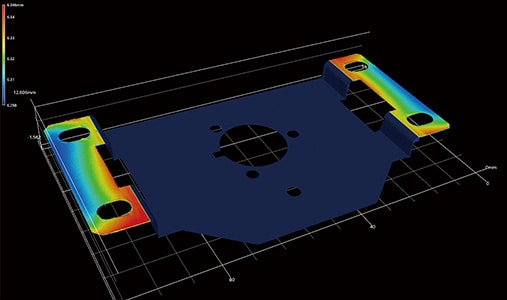
A diferencia de una máquina de medición de coordenadas o un instrumento de medición de imágenes CNC, la Serie VR extrae las características del objetivo colocado en la plataforma y realiza automáticamente la corrección de la posición. El posicionamiento estricto que antes requería mucho tiempo y esfuerzo ya no es necesario. Esto hace posible que cualquier tipo de operador, independientemente de su nivel de experiencia, pueda realizar mediciones de forma fácil e instantánea.
Con la Serie VR, incluso el paralelismo de objetivos con formas complejas puede medirse con precisión simplemente colocando el objetivo en la plataforma y presionando un botón.
Ventaja 2 de la Serie VR: es posible la comparación cuantitativa y el análisis de múltiples conjuntos de datos de medición.
La Serie VR puede medir la forma tridimensional de todo el objeto mediante el escaneado tridimensional de la superficie del objeto en tan solo un segundo. Esto permite medir un gran número de objetivos sin necesidad de preparar la muestra. No es necesario configurar las ubicaciones de medición ni el número de puntos de medición, ya que el sistema establecerá automáticamente las condiciones de medición por usted.
Se pueden mostrar varios conjuntos de datos de medición en una lista y aplicar el mismo contenido de análisis a todos los conjuntos de datos al mismo tiempo.
Las diferencias en los datos de forma de varios objetivos pueden confirmarse de un vistazo. Esto permite realizar análisis por lotes del paralelismo en múltiples conjuntos de datos, y realizar fácilmente una evaluación cuantitativa de cuánto se deforma una pieza NG en comparación con una pieza OK.
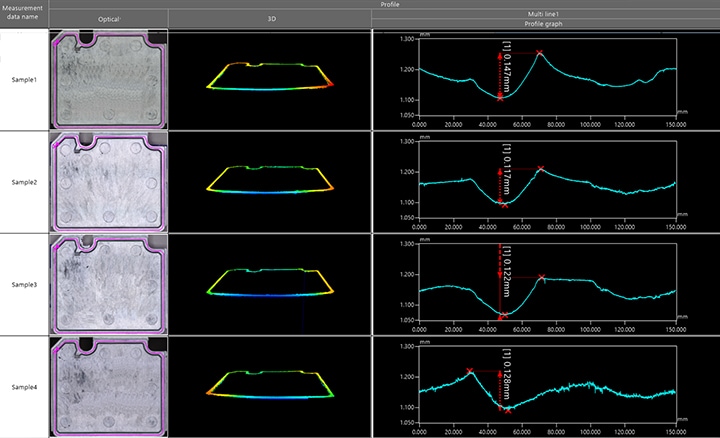
Una amplia variedad de herramientas de ayuda permite configurar fácilmente los contenidos de medición deseados.
Además de su fácil configuración, las herramientas de ayuda permiten incluso a los usuarios principiantes realizar mediciones de formas con rapidez y precisión. Como resultado, se puede aumentar fácilmente el número de muestras no solo para prototipos y pruebas, sino también para la medición e inspección de productos.
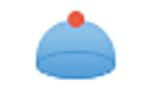
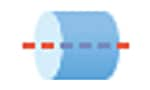
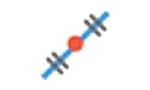
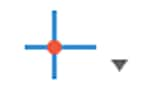
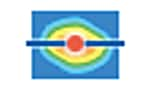
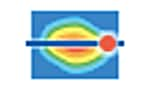
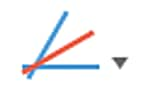
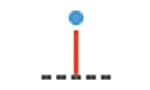
Resumen: mejora integral y mayor eficacia para problemas en la medición del paralelismo de productos conformados en prensa
La Serie VR puede medir formas de objetivos 3D de forma precisa e instantánea mediante escaneado 3D de alta velocidad sin entrar en contacto con el objetivo. La medición del paralelismo puede completarse instantáneamente para piezas pequeñas, piezas grandes y piezas con formas complejas. Estos productos pueden resolver todos los problemas que plantean los instrumentos de medición convencionales.
- Dado que los datos de toda la superficie pueden captarse sin contacto, es posible medir secciones transversales a las que no llega un lápiz óptico. El paralelismo puede medirse con facilidad y precisión incluso en piezas pequeñas.
- Una amplia variedad de herramientas de asistencia resuelven el problema de la variación de los valores de medición causada por factores humanos. Esto permite realizar una verdadera medición cuantitativa.
- Sin necesidad de posicionamiento ni otro tipo de preparación, la medición puede realizarse simplemente colocando el objetivo en la plataforma y presionando un botón. Esto elimina la necesidad de asignar un operador especializado para los trabajos de medición.
- Las formas 3D pueden medirse fácilmente a altas velocidades con gran precisión. Esto permite medir un gran número de objetivos en poco tiempo, lo que contribuye a mejorar la calidad.
Este sistema también permite realizar comparaciones con datos de formas 3D y datos CAD anteriores, así como analizar fácilmente datos como la distribución dentro de las tolerancias. Puede utilizarse eficazmente para una amplia gama de fines, como el desarrollo de productos, el análisis de tendencias de fabricación y las inspecciones por muestreo.
- Perfilómetro óptico 3D de la Serie VR para mediciones de mayor definición y precisión
-