Medición fácil y precisa de conos
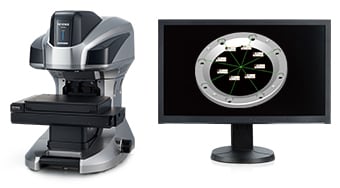
Conicidad es un término utilizado para describir el estrechamiento de un objeto o superficie. Esta página presenta los conceptos básicos de los conos, incluida su finalidad, los tipos de piezas que los utilizan, los métodos para calcularlos, cómo se fabrican y los problemas y soluciones habituales asociados a su medición.
- Conos
- Piezas en las que se utilizan conos
- Cálculo del ángulo de conicidad
- Métodos de producción de conos
- Problemas de la medición convencional de conicidad
- Solución a problemas de medición de conicidad
- Resumen: una mejora y mayor eficacia en la medición de conicidades
Conos
La conicidad indica las condiciones en las que el diámetro, la anchura o el espesor de una estructura larga y estrecha se reduce gradualmente hacia la punta. Hay muchos tipos diferentes de formas cónicas, que se seleccionan en función de la finalidad de uso. Las conicidades se utilizan para reforzar una estructura o facilitar su ajuste, y se forman mediante procesos como el prensado o el corte.
Añadir una forma cónica a un diseño se denomina ahusamiento. Un ángulo de conicidad grande se denomina conicidad aguda, y un ángulo de conicidad pequeño se denomina conicidad suave. Pendiente es un término similar a conicidad, y es necesario utilizar cada uno de estos términos correctamente.
Diferencia entre conicidad y pendiente
Una forma que tiene un ángulo de inclinación en ambos lados es un cono, mientras que una forma que tiene un ángulo de inclinación en un lado mientras que el otro lado es plano es una pendiente. Por ejemplo, observando la misma forma de cono circular, cuando se describe la inclinación de un lado solo utilizando la línea central como referencia, entonces se trata de una pendiente. Cuando se describe la inclinación de ambos lados, entonces se trata de una conicidad.
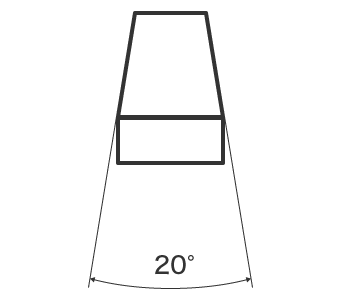
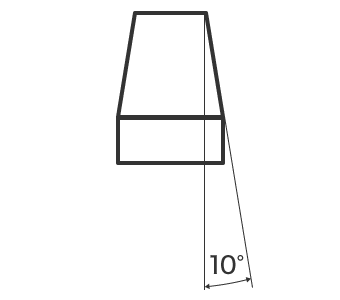
Notación de dibujo para conicidad e inclinación
La inclinación y la pendiente se indican mediante un símbolo y un valor numérico. El tamaño del cono se indica mediante el ángulo o la relación del cono. La pendiente se indica mediante un número denominado relación de pendiente.
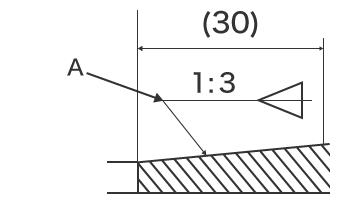
- A
- Alinee el símbolo del cono en la misma dirección que la forma del cono.
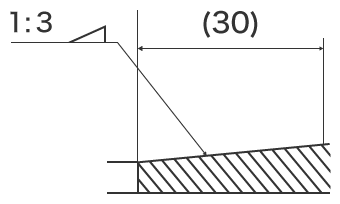
Piezas en las que se utilizan conos
Los conos se utilizan en un gran número de piezas, como rodamientos que soportan pasadores o ejes, tuberías y disipadores de calor o bridas. Todas las formas son cónicas, pero sus fines son distintos y sus formas tienen características diferentes.
Tornillos, rodamientos, piezas de ajuste, etc.
Estas piezas utilizan un cono (cono lineal) que modifica el diámetro linealmente a lo largo de la distancia. El ángulo lateral es constante, y el tamaño de la conicidad se indica mediante el ángulo de conicidad o la relación de conicidad.
Aletas de refrigeración del motor y disipadores térmicos
Estas piezas utilizan un cono (cono exponencial) que modifica el diámetro exponencialmente con la distancia. La forma lateral se estrecha más rápidamente a distancias más alejadas de la base, y la punta es muy afilada. Esto permite reducir el paso y también el peso y las vibraciones.
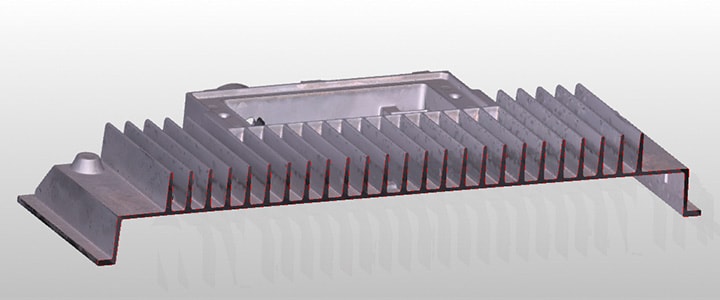
Además, un cono con forma parabólica (cono parabólico) se utiliza en piezas destinadas a reducir la resistencia de los fluidos, como tuberías y carrocerías de aviones. En piezas como los pasadores, que se utilizan para unir otras piezas, se utiliza un cono inverso. Un cono invertido tiene una forma invertida respecto a un cono normal y una punta más gruesa que la base.
Cálculo del ángulo de conicidad
En los dibujos, el tamaño del cono suele indicarse mediante la relación de conicidad. Sin embargo, en casos como el mecanizado con torno, puede ser necesario conocer el valor del ángulo del cono.
Relación de conicidad
Es la relación entre la dimensión del extremo grueso y la dimensión del extremo fino. Por ejemplo, cuando la relación de conicidad es de 3:100, el diámetro se adelgaza 3 mm (0.12") por cada 100 mm (3.94") de longitud.
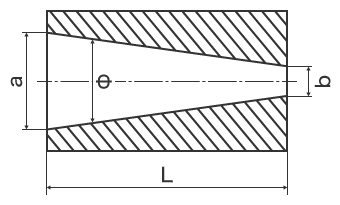
- a
- Mayor diámetro lateral
- b
- Diámetro lateral menor
- L
- Longitud
- Φ
- Ángulo de conicidad
Ángulo de conicidad
El ángulo de conicidad puede calcularse mediante la siguiente fórmula.
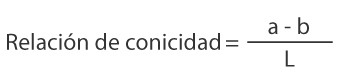

Por ejemplo, cuando la relación de conicidad especificada en el dibujo es 3/100, el ángulo de conicidad puede calcularse como se muestra a continuación.

Métodos de producción de conos
Las conicidades se crean utilizando un torno o una prensa. Con el conformado a presión, la forma cónica se crea al fabricar el troquel y esa forma se "presiona" a continuación sobre un material. En el caso de un torno, el mecanizado se realiza ajustando el ángulo del portaplaquitas. Aquí presentaremos cómo se crea un cono cuando se utiliza un torno.
Un torno es una máquina herramienta que arranca material mientras gira. Se aplica un inserto o una herramienta de corte especializada a la superficie del objeto a medida que gira, y se retira material circunferencialmente. Dado que el corte se realiza mientras la pieza gira, este método es adecuado para el mecanizado de conos en los que el diámetro se hace más fino hacia la punta. Con un torno, el ángulo de la fresa cónica se especifica como 1/2 del ángulo del cono. 1/2 del ángulo de conicidad es igual al ángulo de inclinación.
(1) Gire el torno y ajuste el ángulo.
↓
(2) Accione el mango del torno y realice el corte.
↓
(3) Después de cortar hasta el final, vuelva hasta que se desenganche la broca de la herramienta.
↓
(4) Repita este procedimiento hasta obtener la forma deseada.
Cuando se utiliza un torno de alta precisión, es posible realizar mecanizados cónicos finos del orden de micrómetros. En consecuencia, se necesitan instrumentos de medición de alta precisión para el control de calidad.
Problemas de la medición convencional de conicidad
Es extremadamente importante confirmar que las dimensiones y formas producidas por el mecanizado cónico están dentro de las tolerancias. En particular, dado que un cono cónico es una forma tridimensional, se requiere una medición tridimensional cuantitativa y de alta precisión. Sin embargo, existen diversos problemas de medición cuando se utilizan comparadores ópticos convencionales, sistemas de medición de perfiles y calibres cónicos. Estos problemas pueden incluir la dificultad para lograr una medición precisa y la variación de los valores medidos.
Problemas en la medición de la conicidad mediante un comparador óptico
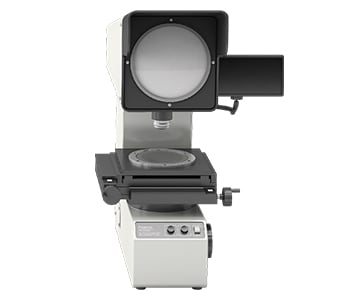
Un comparador óptico es un tipo de instrumento de medición óptica con un principio de medición similar al de un microscopio óptico. Se coloca un objeto en un escenario y el instrumento de medición transmite luz desde abajo, proyectando el perfil del objeto en una pantalla. Algunos comparadores ópticos de gran tamaño tienen diámetros de pantalla superiores a 1 m (3.3 pies). En el caso de piezas con conos rebajados, el perfil no puede visualizarse con este método sin cortar antes la muestra.
Este método de medición plantea los siguientes problemas.
- Con una lente de comparador óptico normal, solo una parte del objetivo está enfocada. Por este motivo, es necesario enfocar con precisión cada punto de medición manualmente. Por ejemplo, cuando el objetivo es un cono circular, es necesario ajustar con precisión el enfoque en cada punto de medición. Esto no solo da lugar al problema del error de medición cuando la posición del enfoque difiere en función del operador, sino también al problema del mayor tiempo necesario para ajustar el enfoque cuando se miden más ubicaciones. También puede ser necesario cortar el objetivo para medir la forma de la sección transversal.
- Al comparar formas, es necesario comprobar visualmente las diferencias superponiendo la proyección con un dibujo ampliado 10×. Las diferencias entre las dimensiones proyectadas y el plano no pueden obtenerse de forma numérica, y la forma del perfil debe transferirse a papel de calca, lo que dificulta el almacenamiento y la comparación de los datos.
Esto da lugar a una serie de grandes problemas. No todos los operadores in situ son capaces de medir con precisión las formas. También hay algunos lugares que no se pueden medir y puede ser necesario recortar el objetivo.
Problemas en la medición de conicidades mediante un sistema de medición de perfiles
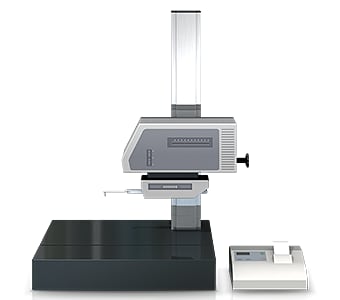
Un sistema de medición de perfiles mide y registra el perfil de un objetivo trazando su superficie con un lápiz óptico. En los últimos años, se han desarrollado sistemas de medición de perfiles que utilizan un láser en lugar de un lápiz óptico para medir formas complejas trazando el perfil sin contacto. Algunos modelos son incluso capaces de realizar mediciones tanto de la superficie superior como de la inferior.
Un sistema de medición de perfiles debe trazar una línea de medición precisa en la dirección perpendicular relativa a la forma cónica objetivo.
Esto plantea los siguientes problemas.
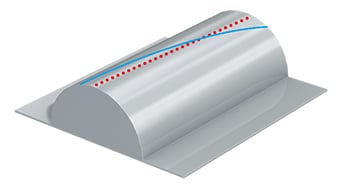
- El trabajo de medición requiere mucho tiempo, incluido el tiempo necesario para fijar la muestra a la plantilla y nivelarla. También se requieren conocimientos y habilidades relacionados con el uso de sistemas de medición de perfiles para nivelar un objetivo con precisión.
- El lápiz óptico de un sistema de medición de perfiles se mueve hacia arriba y hacia abajo en un arco centrado en el fulcro del brazo del lápiz óptico, y la punta del lápiz óptico también se mueve en la dirección del eje X. Esto produce error en los datos del eje X.
- Trazar la línea deseada con el lápiz óptico es un trabajo extremadamente difícil, e incluso un ligero desplazamiento del lápiz óptico produce errores en los valores medidos.
Solución a problemas de medición de conicidad
Al repasar los problemas de los instrumentos de medición convencionales, se observa que todos ellos tienen un punto en común. Se trata de que la medición de un objetivo o área tridimensional se realice mediante el contacto de puntos y líneas.
Para resolver estos problemas de medición, KEYENCE ha desarrollado el perfilómetro óptico 3D de la Serie VR. La Serie VR captura con precisión la forma tridimensional de toda la superficie del objetivo sin entrar en contacto con él. También mide la forma tridimensional mediante el escaneado tridimensional del objetivo en el escenario en tan solo un segundo con gran precisión. Esto permite una medición cuantitativa instantánea y sin variaciones en los resultados de la medición. A continuación se explican algunos ejemplos concretos de las ventajas.
Ventaja 1: medir sin cortar el objetivo
Con un instrumento de medición de tipo contacto, como la sonda no puede llegar hasta el fondo, es difícil medir objetivos cuyo paso es pequeño y en los que hay rebajes, como las herramientas de álabes y las aletas del disipador térmico.
La Serie VR puede medir conos y otras formas seccionando virtualmente el objeto, algo que antes requería cortarlo. Incluso los objetos con zonas rebajadas pueden medirse sin destruirlos.
Los usuarios también pueden crear plantillas para los elementos que se miden con más frecuencia con el fin de agilizar el proceso de medición y analizar rápidamente varias piezas.
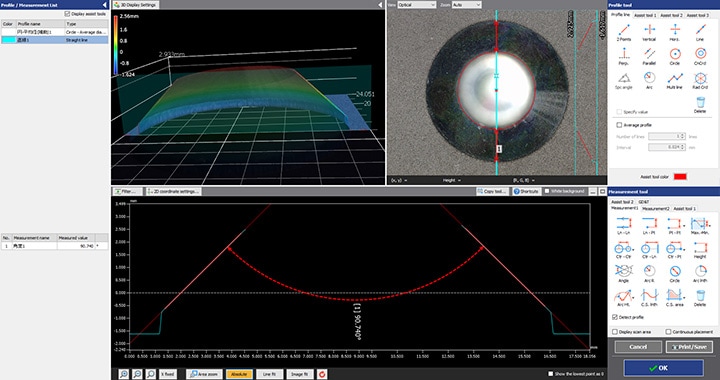
Ventaja 2: mide un área grande de hasta 300 x 150 mm (11.81" × 5.91")
La medición puede realizarse simplemente colocando el objetivo en la plataforma y presionando un botón. No es necesaria una colocación estricta ni ningún otro tipo de preparación. La Serie VR es capaz de extraer características del objeto y ajustar automáticamente la alineación de la pieza. Esto permite realizar mediciones de gran precisión por operadores que no tienen conocimientos ni experiencia relacionados con los instrumentos de medición.
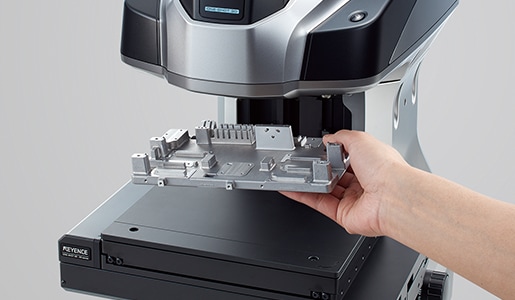
Resumen: una mejora y mayor eficacia en la medición de conicidades
La Serie VR resuelve los problemas a los que se enfrentan los instrumentos de medición convencionales mediante la medición instantánea de objetos 3D con escaneado 3D de alta precisión y sin contacto.
- Medir secciones transversales sin cortar el objetivo.
- Eliminar las variaciones derivadas de factores humanos, haciendo posible una verdadera medición cuantitativa.
- Sin necesidad de un posicionamiento preciso u otro tipo de preparación, la medición puede realizarse simplemente colocando el objetivo en la plataforma y presionando un botón. Esto elimina la necesidad de asignar un operador especializado para los trabajos de medición.
- Las formas 3D pueden medirse fácilmente a altas velocidades con gran precisión. Esto permite medir un gran número de objetivos en poco tiempo, lo que contribuye a mejorar la calidad.
Este sistema también permite realizar comparaciones con mediciones 3D y datos CAD anteriores, así como analizar fácilmente los datos, como la distribución dentro de las tolerancias. Puede utilizarse eficazmente para una amplia gama de fines, como el desarrollo de productos, el análisis de tendencias de fabricación y las inspecciones por muestreo.