Un método de medición instantánea y precisa de la textura superficial
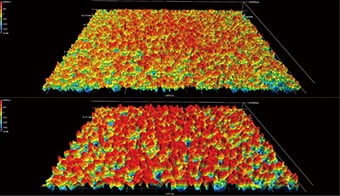
Se denomina textura superficial al dibujo de la veta natural de la madera o el cuero comparado con el de la superficie del metal, el plástico, el cristal, la piedra u otro material. Además de un tacto de alta calidad y un valor añadido, también se añade textura a la superficie para mejorar la durabilidad y la seguridad. Se utiliza en una amplia gama de productos, incluidos equipos de oficina como computadoras personales e impresoras, paneles de instrumentos de automóviles, teléfonos móviles y consolas de videojuegos residenciales.
Aquí explicaremos los principios, puntos clave y otros aspectos básicos cuando se trata de la producción de moldes de texturizado. Abordaremos problemas comunes en su medición y posibles soluciones a estos problemas.
- Textura de la superficie
- Principios de la producción de moldes para texturización de superficies
- Puntos clave para la texturización de superficies
- Problemas de las mediciones convencionales de la textura superficial
- Solución de problemas en la medición de la textura superficial
- Resumen: una mejora y mayor eficacia en la medición de texturas superficiales difíciles
Textura de la superficie
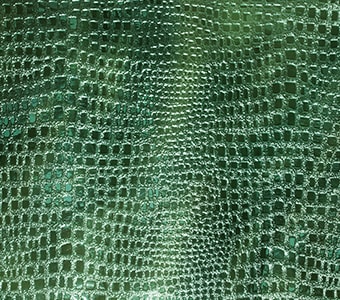
Es probable que haya visto las palabras "textura superficial" en la descripción de una superficie de cuero. El texturizado de superficies confiere a la superficie de un producto un veteado de madera natural, un patrón de cuero o un patrón mate. Puede prolongar la vida útil del producto, mejorar su aspecto y producir una sensación de alta calidad.
El proceso de aplicación de textura durante la producción se denomina texturizado de la superficie. También se denomina satinado o grabado. Estas texturas pueden crearse con moldes (cavidad o núcleo) mecanizados con el patrón de textura en él, que luego se transfiere a la superficie del producto durante el moldeo, el grabado químico que utiliza productos químicos para disolver el metal y el chorro de arena.
Principios de la producción de moldes para texturización de superficies
La textura de la superficie se produce transfiriendo al producto un patrón mecanizado en el molde de texturizado. Por este motivo, un molde de texturizado debe mecanizarse minuciosamente para reproducir una textura tridimensional lo más parecida posible a la real. Esto se consigue repitiendo los procesos de transferencia y grabado. Los fundamentos del procesamiento son los mismos independientemente del patrón que se reproduzca. Este proceso se explica mediante las figuras de sección transversal que figuran a continuación.
-
Primer traslado
-
Primer grabado
- A
- Molde
- B
- Tinta resistente al ácido
- C
- El metal de las partes en las que no se aplica tinta resistente al ácido se erosiona y se elimina.
-
Segunda transferencia
-
Segundo grabado
- A
- Molde
- B
- Tinta resistente al ácido
- C
- La parte eliminada en el primer grabado se vuelve aún más profunda.
- D
- Parte eliminada en el segundo grabado
-
Tercera transferencia
-
Tercer grabado
- A
- Molde
- B
- Tinta resistente al ácido
- C
- Parte recién retirada en el tercer grabado
De este modo, la transferencia y el grabado repetidos crean un molde texturizado con una textura muy expresiva que da sensación de tridimensionalidad. El proceso puede realizarse una vez para un patrón de textura simple, o puede repetirse diez veces o más para un patrón complejo.
En el texturizado de superficies, casi el 80% de todo el proceso es trabajo manual. El traslado, en particular, requiere técnicas artesanales y un trabajo arduo, y se necesitan muchas horas de mano de obra.
Puntos clave para la texturización de superficies
En la mayoría de los casos, el texturizado de la superficie se realiza una vez finalizados los trabajos de mecanizado y pulido. Por ello, cuando es necesaria una corrección o se produce un defecto que no puede corregirse, puede tener un grave efecto adverso en el programa de producción. Por este motivo, puede comprender que el texturizado de superficies es un proceso final que entraña un riesgo muy grande.
A continuación se indican los puntos clave que requieren atención en el texturizado ordinario de superficies para reducir el riesgo de aparición de defectos.
Pulir la superficie del molde con papel de lija o granos abrasivos.
Eliminar completamente las microfisuras en el molde y la capa mecanizada de la superficie.
Prevenir los defectos causados por el material del molde.
Para el molde, seleccione un material de acero que tenga un bajo riesgo de defectos de material como huecos (burbujas), impurezas o carburos.
Para el tratamiento térmico del material de acero, asegúrese de que la dirección de corte y la dirección de laminación son las mismas siempre que sea posible
Si las direcciones no son las mismas, pueden producirse desigualdades y puede resultar imposible obtener una textura uniforme. Además, también es importante que el texturizado no se aplique en lugares donde se haya realizado una reparación por soldadura.
Preste atención al ángulo de calado y al espesor.
Ajuste ángulos de calado lo más grandes posible. Al procesar los laterales del molde, aumente también el espesor del producto moldeado para aumentar deliberadamente la contracción. Controle la temperatura de la superficie del molde cuando sea posible utilizando una estructura de refrigeración y un calentador de cartucho.
También puede mejorarse la calidad modificando el proceso para que el mecanizado se realice después del texturizado de la superficie. El aspecto final de la textura de la superficie cambia visualmente en función de factores como el tipo de material de moldeo, la coloración y el contenido de fibra de vidrio. Por este motivo, consulte datos anteriores y seleccione el tipo de textura, la profundidad y otras características en consecuencia.
Problemas de las mediciones convencionales de la textura superficial
En cuanto a la textura de la superficie, la profundidad, la altura y la forma del dibujo influyen mucho en la calidad del producto. Los defectos de textura de la superficie no solo afectan al aspecto y al tacto. En el caso de la textura superficial para evitar el deslizamiento, los defectos pueden afectar a la seguridad y al agarre general de una pieza. En el caso de la textura destinada a ocultar defectos superficiales, los defectos pueden afectar a la productividad. Por esta razón, la medición y la inspección son necesarias para confirmar que la textura de la superficie en toda la superficie es la prevista.
Convencionalmente, se utilizan microscopios y rugosímetros para realizar la medición y cuantificación de la textura. Sin embargo, estos métodos de medición presentan algunos problemas comunes.
Problemas en la medición de la textura superficial mediante un rugosímetro o un sensor de desplazamiento
Al medir la rugosidad superficial con un rugosímetro, la medición en la dirección de la altura se limita únicamente a puntos o líneas. En consecuencia, es necesario aumentar el número de puntos de medición para identificar con precisión la forma. El tiempo que se tarda en adquirir las mediciones realizadas moviendo una sonda o un lápiz óptico aumenta en proporción al número de puntos de medición. Además, como es necesario corregir el posicionamiento después de instalar el objetivo, los valores medidos carecen de fiabilidad porque los puntos de medición varían en función del operador.
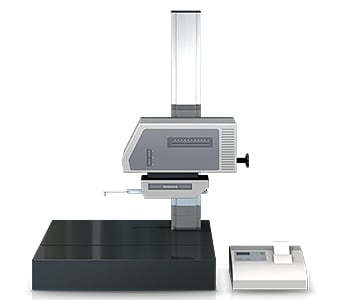
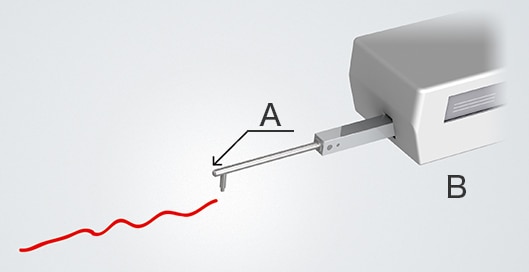
- A
- Sonda
- B
- Detector
Problemas en la medición de la textura superficial mediante microscopio
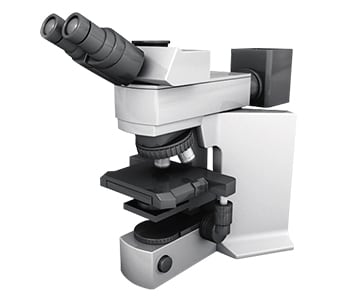
A diferencia de los rugosímetros, los microscopios pueden captar información "superficial". La anchura de las ranuras puede medirse determinando la cantidad de movimiento de la plataforma, y la profundidad también puede medirse determinando la cantidad de cambio de enfoque.
Al mismo tiempo, las mediciones dependen del ojo humano, lo que provoca variaciones debidas a las diferencias de criterio de los operadores. Otra preocupación es que los microscopios no están pensados originalmente para medir. Puede que no sea posible cuantificar los resultados de la medición, o que la fiabilidad de los valores de medición cuantificados sea baja.
Solución de problemas en la medición de la textura superficial
Las herramientas de medición que se utilizan tradicionalmente para analizar la textura de las superficies encuentran problemas en la medición de objetivos y áreas tridimensionales. Estas mediciones se realizan mediante contacto puntual o lineal, lo que se traduce en una baja fiabilidad. Para resolver estos problemas de medición, KEYENCE ha desarrollado el perfilómetro óptico 3D de la Serie VR.
La Serie VR captura con precisión la forma 3D de toda la superficie sin entrar en contacto con el objetivo. También mide la forma 3D escaneando el objetivo en el escenario en tan solo un segundo con gran precisión. Es capaz de realizar mediciones instantáneas y cuantitativas. Esta sección presenta algunas ventajas específicas de la Serie VR.
Ventaja 1: capaz de medir un área amplia de hasta 200 x 100 mm (7.87" × 3.94").
La medición puede realizarse colocando el objetivo en la plataforma y presionando un botón. No es necesaria una colocación estricta ni ningún otro tipo de preparación. Esto ayuda a garantizar que todos los operadores, independientemente de su nivel de habilidad, podrán obtener resultados precisos y repetibles.
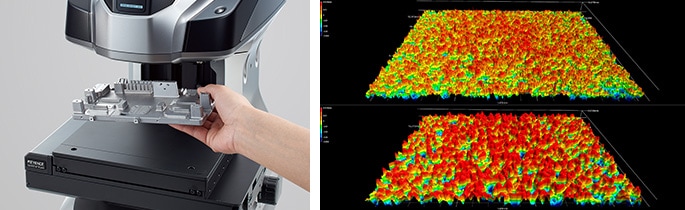
A diferencia de los instrumentos de medición convencionales, la Serie VR es capaz de medir fácilmente parámetros de altura de textura superficial distribuidos en una amplia zona, algo que antes requería mucho tiempo y esfuerzo para medir. También se incluyen herramientas informáticas que permiten realizar fácilmente diversas mediciones. Esto hace posible que incluso un operador que no esté familiarizado con los principios de medición pueda realizar análisis de forma fácil e instantánea. Esto elimina la necesidad de asignar un operador especializado a la herramienta.
Ventaja 2: el sistema de medición admite la trazabilidad.
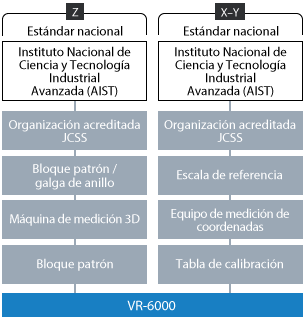
La Serie VR es una máquina de medición de coordenadas sin contacto que garantiza la trazabilidad según las normas nacionales. El rendimiento del sistema está garantizado tanto en precisión como en repetibilidad, lo que produce resultados de medición altamente fiables en los que puede confiar. Los certificados de calibración vienen de serie con la unidad principal y la placa de calibración.
También viene de serie un calibrador de calibración que incluye un informe de inspección y un certificado de calibración. El medidor está vinculado a la escala de referencia utilizada por los laboratorios de certificación del JCSS. Como resultado, cualquier usuario puede realizar la calibración in situ con facilidad y precisión sin necesidad de llamar a un técnico para que le ayude.
Resumen: una mejora y mayor eficacia en la medición de texturas superficiales difíciles
La Serie VR puede medir formas de objetivos en 3D de forma precisa e instantánea mediante un escaneado rápido y sin contacto. Incluso mediciones difíciles como la altura y la rugosidad de la textura de la superficie pueden realizarse en tan solo un segundo. La Serie VR puede ayudar a resolver los numerosos problemas con los que se encuentran las herramientas de medición convencionales.
- Dado que mide toda la superficie, la Serie VR puede medir fácilmente la textura de la superficie en un área amplia. También puede medir diversos parámetros de rugosidad.
- De este modo se elimina la variación derivada de factores humanos, lo que hace posible una verdadera medición cuantitativa.
- Sin necesidad de posicionamiento u otro tipo de preparación, la medición puede realizarse simplemente colocando el objetivo en la plataforma y presionando un botón. Esto elimina la necesidad de asignar un operador especializado para los trabajos de medición.
- Las formas 3D pueden medirse fácilmente a altas velocidades con gran precisión. Esto permite medir un gran número de objetivos en poco tiempo, lo que contribuye a mejorar la calidad.
Este sistema también permite la comparación pieza a pieza y CAD a pieza. Los usuarios también pueden realizar fácilmente análisis de datos y asignar tolerancias para obtener resultados claros de aprobado/no aprobado. Puede utilizarse eficazmente para una amplia gama de fines, como el desarrollo de productos, el análisis de tendencias de fabricación y las inspecciones por muestreo.