Marcado láser de Códigos 2D (Datamatrix / Código QR / Código de barras)
Si bien, la demanda por productos más pequeños y delgados, y por una trazabilidad más detallada continúan creciendo, hay una necesidad cada vez mayor de empaquetar más información dentro de un espacio limitado en los productos manufacturados.
Un código 2D puede contener de decenas a cientos de veces la información de un código de barras. Esta alta densidad de información permite que un código 2D contenga la misma cantidad de información que un código de barras en tan sólo 1/30 del tamaño. Estas características ventajosas han llevado a expandir las aplicaciones en varios campos.
- Ejemplos de aplicación de código 2D
- Clasificación de códigos 2D
- Función de marcado 3D
- Profundidad de foco
- Patrones de marcado
Ejemplos de aplicación de código 2D
El uso de códigos 2D simplifica la administración, mejora la precisión y reduce las horas de trabajo. En los últimos años, se exige una trazabilidad detallada, no sólo para los productos terminados, sino también para las partes individuales. El número de códigos 2D marcados directamente con marcadora láser está aumentando. En consecuencia, se requiere un marcado de alta calidad para garantizar una lectura de códigos 2D estable.
Industria de dispositivos electrónicos
- Unidad de cámara
-
- Los códigos 2D permiten un control en serie de piezas pequeñas con espacio de marcado limitado. Esto permite flexibilidad para mantener el ritmo, con un control de calidad cada vez más estricto.
- Marcapasos
-
- Los historiales de fabricación e inspección se pueden almacenar en códigos 2D, para una gestión de la trazabilidad. Se puede revisar el historial rápidamente, simplemente leyendo el código.
Industria automotriz
- Bloque de cilindros
-
- En cada producto se marca un número de serie con un código 2D. El código se lee en procesos posteriores para proporcionar instrucciones de trabajo a los robots.
- Inyección
-
- Los datos históricos, que incluyen la fecha de fabricación e información de la línea, están marcados en cada producto con un código 2D, y se utilizan para la gestión de trazabilidad.
Clasificación de códigos 2D
Para garantizar una lectura estable, es importante proporcionar un marcado, que los lectores de códigos 2D puedan leer fácilmente. Existen algunos estándares para la lectura de códigos 2D, que se pueden emplear como guía. La facilidad de lectura se puede expresar con calificaciones. Un estándar llamado ISO/IEC TR 29158 (AIM DPM-1-2006)* se usa generalmente para valorar el marcado directo de productos con marcadores láser. Esta norma especifica los siguientes criterios para la evaluación de calificaciones de lectura.
Esta es una norma internacional para códigos 2D, que evalúa la calidad del marcado directo de partes.
- 1Valoración total (todos)
-
La valoración total se determina como el grado más bajo entre los criterios 2 a 11. El resultado se expresa como una calificación de letras de A a D o F, donde A es la calificación más alta (estabilidad de lectura).
- 2Decodificación exitosa/fallida (DEC)
-
Evaluación de si la decodificación (lectura) es posible o no
- 3Contraste de celda (CC)
- Diferencia en los valores de intensidad de luz promedio entre las celdas brillantes y las oscuras
- 4Modulación de celda (CM)
- Evaluación de la variación en el brillo de las celdas brillantes y las oscuras.
- 5Margen de reflexión (RM)
Evaluación mediante la adición de la precisión de valoración de las celdas brillantes y las oscuras a CM (4).
- 6Daño al patrón fijo (FPD)
-
Grado de daño al patrón fijo (ver la figura a continuación)
- 7Daño a la información del formato (FID)
-
Grado de daño a la información de formato de un código QR (ver la figura a continuación)
- 8Daño a la información de versión (VID)
-
Grado de daño a la información de versión de un código QR (Modelo 2 versión 7 y posterior)
- 9Desuniformidad axial (AN)
-
Grado de distorsión de los tamaños vertical y horizontal de un código
- 10Desuniformidad del cuadriculado (GN)
-
Evaluación de la mayor desalineación entre las posiciones de las celdas.
- 11Corrección de errores no utilizados (UEC)
-
Relación de correcciones de errores que no se utilizan para la decodificación
En el marcado directo de piezas sobre superficies metálicas, los valores CC, CM, RM y FPD a menudo son más bajos, cuando no se puede obtener contraste. El evitar que estos valores disminuyan es la meta, para garantizar un marcado legible. En los últimos años, se exige un grado C o superior, en la mayoría de los casos. Es deseable lograr calificaciones más altas, inmediatamente después del marcado.
Función de marcado 3D
La diferencia de contraste entre las celdas negras y las blancas es importante en la valoración de los códigos 2D. Un marcadora láser produce diferentes colores, cambiando las condiciones al realizar un marcado blanco o uno negro.
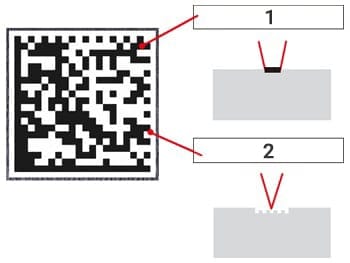
- 1. Marcado negro recocido (oxidación)
- Cuando se aplica el rayo láser al objeto a marcar, el foco se desplaza de tal modo que sólo se conduzca el calor. Al aplicar calor, sin producir un grabado en el objeto, se forma una película de óxido en la superficie. Esta película es de color negro y representa el marcado negro.
- 2. Grabado blanco
- El rayo láser se aplica al objeto a marcar en el punto focal. La superficie metálica se retira ligeramente para exponer una superficie irregular. Esto causa un reflejo irregular de la luz para crear un marcado de color blanco.
- Tamaño de punto de haz variable
-
- Iluminación en las coordenadas establecidas
El marcado de códigos 2D produce un contraste entre negro y blanco, mediante grabado u oxidación. La clave es emplear para el marcado blanco un enfoque agudo y para el marcado negro un enfoque borroso. Los tamaños de punto de haz variable de la función de marcado 3D ofrecen un método eficaz.
El contraste es importante para el marcado de códigos 2D. La corrección 3D es un método eficaz para mantener el enfoque constante en toda el área.
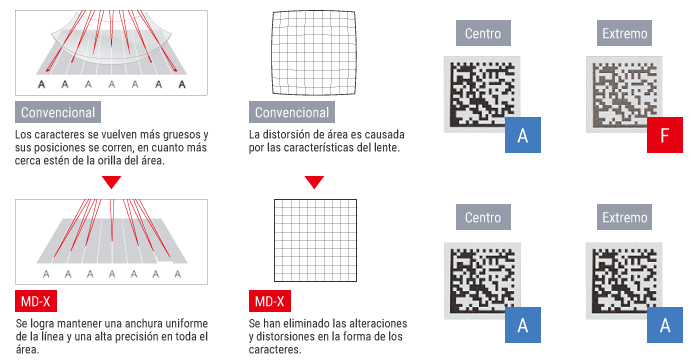
En el centro del área de marcado se logra un marcado ideal, sin ningún problema. Sin la corrección de la función de marcado 3D, puede ser difícil crear un marcado con un contraste claro entre el blanco y el negro, lo que resulta en calificaciones más bajas.
Profundidad de foco
Un rayo láser tiene una profundidad de foco. Cuando el foco se desvía, la calidad del marcado se degrada y esto también afecta la lectura del código 2D.
El código 2D cambia de acuerdo con las distancias focales
A medida que la distancia focal se aleja de la posición de referencia, la marca se desvanece y el contraste disminuye, lo que resulta en calificaciones más bajas. Aunque la profundidad de foco permitida varía según el método de oscilación del láser, es necesario evitar que el foco se desvíe, manteniendo una distancia focal constante entre el objeto y el marcadora láser, o utilizando un sensor de desplazamiento.
- Marcadora láser de fibra de KEYENCE
-
- Marcadora Láser YVO4 de KEYENCE
-
Método de oscilación láser y profundidad de foco
Comparación de la distribución de la potencia del haz
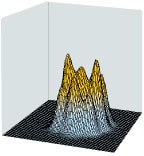
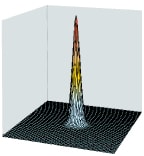
(método de bombeo final)
La figura de la derecha es una comparación de la calidad de marcado entre un láser YVO4 y un láser de fibra. Un láser YVO4 produce un láser con una potencia pico alta y un pulso corto. Esto permite que el láser irradie las partes con una fuerza ideal y una alta densidad de energía en poco tiempo. Incluso cuando el foco se desvía debido al movimiento de los objetos o la tolerancia del producto, su calidad de marcado es estable, en comparación con los tipos de fibra. En los casos en que el marcado se ve afectado por un ángulo incidente, como en el borde de un área de marcado, el láser YVO4 logra una calidad de marcado estable sin desvanecimiento.
Función de autoenfoque
Mecanismo de la función de autoenfoque
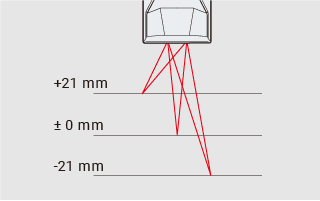
El marcadora láser Serie MD-X de KEYENCE tiene una cámara integrada para ajustar el enfoque automáticamente, sin la necesidad de un dispositivo externo. Mantiene una alta calidad de marcado, incluso en objetos que convencionalmente son difíciles de marcar, debido a una distancia focal inestable. Además, el tiempo para realizar ajustes cuando se cambian los tipos de productos ya no es necesario, lo que reduce considerablemente las horas de trabajo, simplifica las instalaciones y mejora la productividad.
La cámara incorporada se utiliza para monitorear el puntero láser de medición de longitud. La distancia focal se calcula a partir de la posición del puntero, que se utiliza para el enfoque automático. Esta medición puede no ser posible dependiendo del material, la forma o la condición de la superficie del objeto.
Patrones de marcado
El marcador proporciona varios tipos de patrones de marcado de código 2D, a fin de que se logre un marcado óptimo de acuerdo con las diversas condiciones. Los siguientes ejemplos introducen métodos de marcado óptimos, de acuerdo con ciertas condiciones específicas.
Selección de varios patrones de marcado
- 11 tipos de patrones de marcado
-
- 6 tipos de patrones base
-
Marcado de código 2D claro
En algunos objetos, la lectura puede ser inestable debido a la influencia de superficies metálicas con acabado cepillado. El solo hecho de cambiar el patrón de marcado de los códigos 2D o las bases, puede mejorar la velocidad de lectura.
-
Objeto con superficie de metal cepillado
-
Cuando se utiliza la trama horizontal para el procesamiento de la base, la lectura es inestable debido a líneas de cepillado restantes.
-
Cuando se utiliza la trama cruzada en ángulo para el procesamiento de la base, las líneas de cepillado se vuelven invisibles y la lectura es estable.
Marcado de código 2D más rápido
El tiempo para el marcado puede ser limitado, dependiendo del volumen de producción. La selección de un patrón de marcado óptimo permite un tiempo de marcado más corto, así como una mayor productividad.
-
Patrón B - Marcado estándar que marca las celdas una por una de izquierda a derecha
- Tiempo de marcado: 637 ms
-
Patrón entero 2 - Patrón eficiente que marca un código 2D completo en un solo trazo
- Tiempo de marcado: 342 ms
47% de reducción respecto al método convencional
El tiempo se calculó con un ejemplo de marcado de 16 × 16 DataMatrix con un tamaño de celda de 0.3 mm. La evaluación anterior es un caso típico. El resultado varía según el material y las condiciones de la superficie del objeto, así como las condiciones de marcado.
Tallado de códigos 2D
El tallado puede ser necesario en los casos en que se aplica un recubrimiento o endurecimiento después del marcado. Se proporcionan patrones de tallado para permitir un volumen uniforme de tallado simple o profundo en poco tiempo.
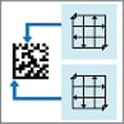
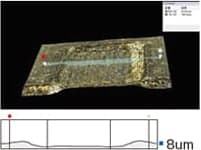
El rayo láser se cruza para que el volumen de tallado sea uniforme.
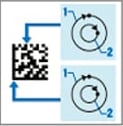
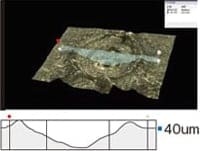
El objeto se talla concéntricamente con un rayo láser, para que el calor acumulado realice un tallado profundo en poco tiempo.